Touring a Lippert RV axle factory
Touring a Lippert RV axle factory
How are RV axles made? We asked that question of our friends at Lippert who offered to show us first-hand in a tour through an axle factory. What does it take to build an axle, or any part for an RV?
Who is Lippert?
Lippert is the largest RV component supplier in the US. If you own an RV made recently, it has Lippert components on it. The company started making chassis for modular homes and, over time, has grown to become a huge supplier or products to the RV industry.
I’m not sure if it’s possible to even buy an RV without having something from Lippert and many RVs have a lot of components by the company.
When you consider the marketing advantage Lippert has you would think that it would be an opportunity to step back on things like quality control, but that’s not the case whatsoever. This is the third Lippert plant I’ve been to and it’s clear that the team is empowered to do their best to create a product that lives up to what it is supposed to do.
One of the things I’ve learned is that Lippert builds products to order. So if you are an RV company and want a specific caliber of product or one that meets a certain level of durability, Lippert will likely build what you want. So if you specify a chassis or axle that meets a minimum specification, you’ll get what you ordered.
If you want something that is going to far exceed a standard, Lippert will build that as well.
Considering that Lippert makes components for Airstream, Rockwood, Grand Design, K-Z, Cherokee and all levels of RVs with all levels of longevity and durability they are highly able to adapt and deliver to what the RV manufacturer specifies.
This is another reason why the company doesn’t do more automation. If you’re only building a few units, they can do that. If you’re building many thousands of units, they can do that. If you want a single example as a preproduction prototype, they can do that. The company is very, very flexible and, again, will deliver what the RV manufacturer specifies.
Build it right
With the flexibility and adaptability of the production process there are a lot of checks and balances in the system. When we toured the chassis factory last year it was very evident that every process had several checks in place to make sure that it was accurate.
This was true of the axle factory as well.
There are robotic welders for some of the pieces including putting the spindles on the end of the axle tubes. Cutting is done in a semi automated process but then checked several times by the team member who is responsible for making the cuts.
We walked through the welding line where there were different levels of welding professionals on hand. Some of the processes are easier and aren’t quite as taxing so someone looking to step into the welding profession might test to see if they can get into this area.
There were also master welders on hand for the more difficult processes. There are a number of steps in place to learn to step into these roles.
Data
One of the things that was also incredible about this experience is the sheer volume of data being generated and tracked. If you look at your RV and find a bar code or label from Lippert, it’s a gateway to some interesting information.
For example, when an axle is made Lippert tracks where the steel came from. They track who cut the axle tube. They track who welded it. They track what parts went onto it and when.
There are so many data points but this enables them to make replacement and maintenance parts available easily. One of the tips we got in Lippert RV Owners School is to take photographs of every sticker and label when your RV is new. That way you have a record of all the various components in the RV.
With an axle, for example, if you have that data tag you can use that to go onto the Lippert store and get replacement brake shoes. If you happen to damage or break a spring, you can get the replacement for that. All the various bits and parts for the axle can be ordered with the information on the little labels on the individual products and components.
What we saw being made
We toured two Lippert plants, the one I’m writing about here is Lippert plant 45. This plant makes a wide assortment of things but it’s neat to know that raw metal comes in one side and finished products come out the other side.
What I saw being made included travel trailer axles, fifth wheel pin boxes, power steps for motorized RVs and the huge cargo door openings for toy haulers.
Specifically the busiest line was the one making axles for travel trailers. The activity level was measured and well paced and the actual creating of the parts was interspersed with measuring all the pieces and components after each step. In fact I think an axle tube was measured something like 8-10 times just in its basic form.
Then it’s measured some more and has to meet the exact specifications set forth by the design.
While watching the team make leaf spring suspension axles was interesting, what truly fascinated me was watching them make torsion axle suspensions.
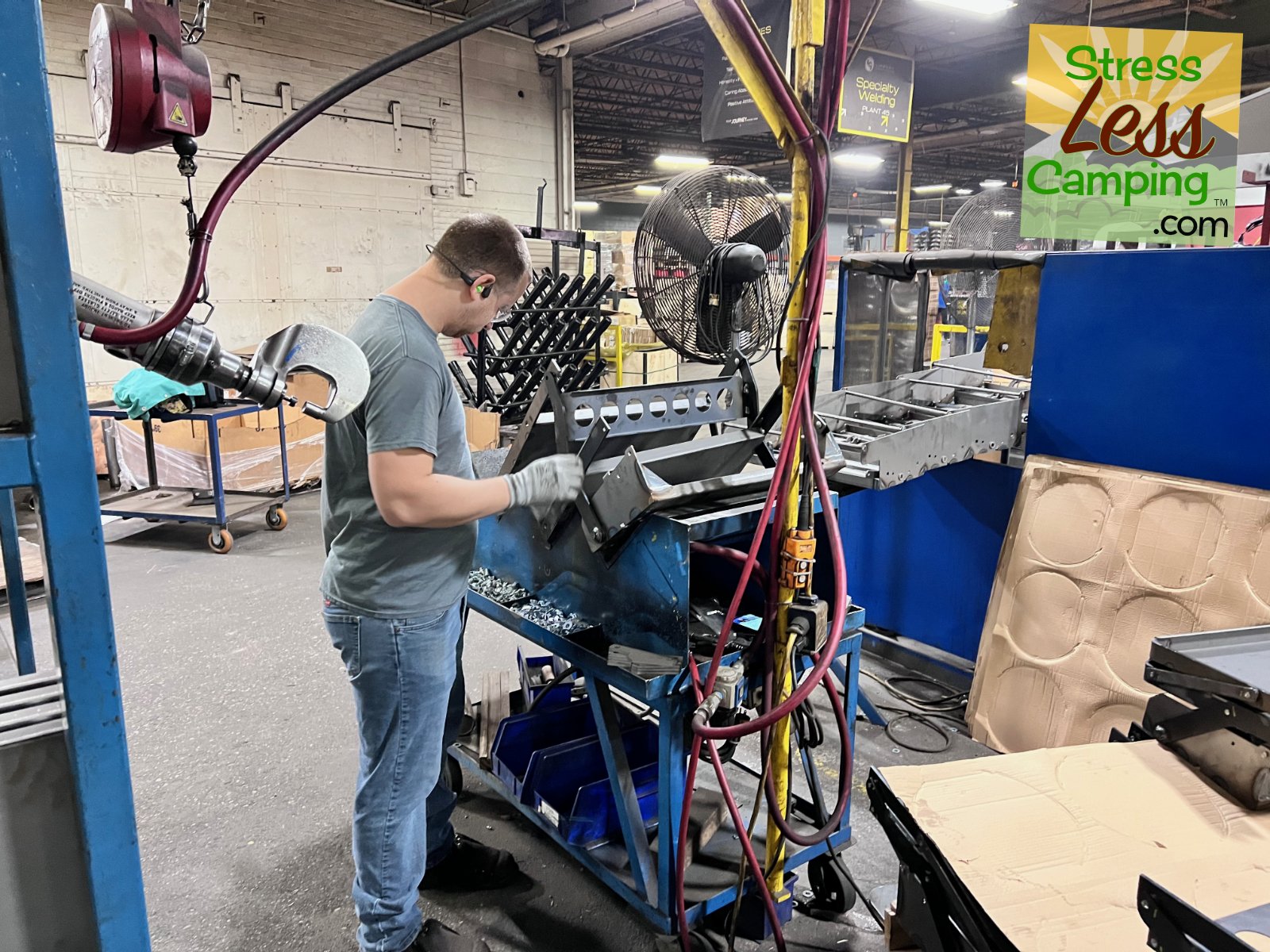
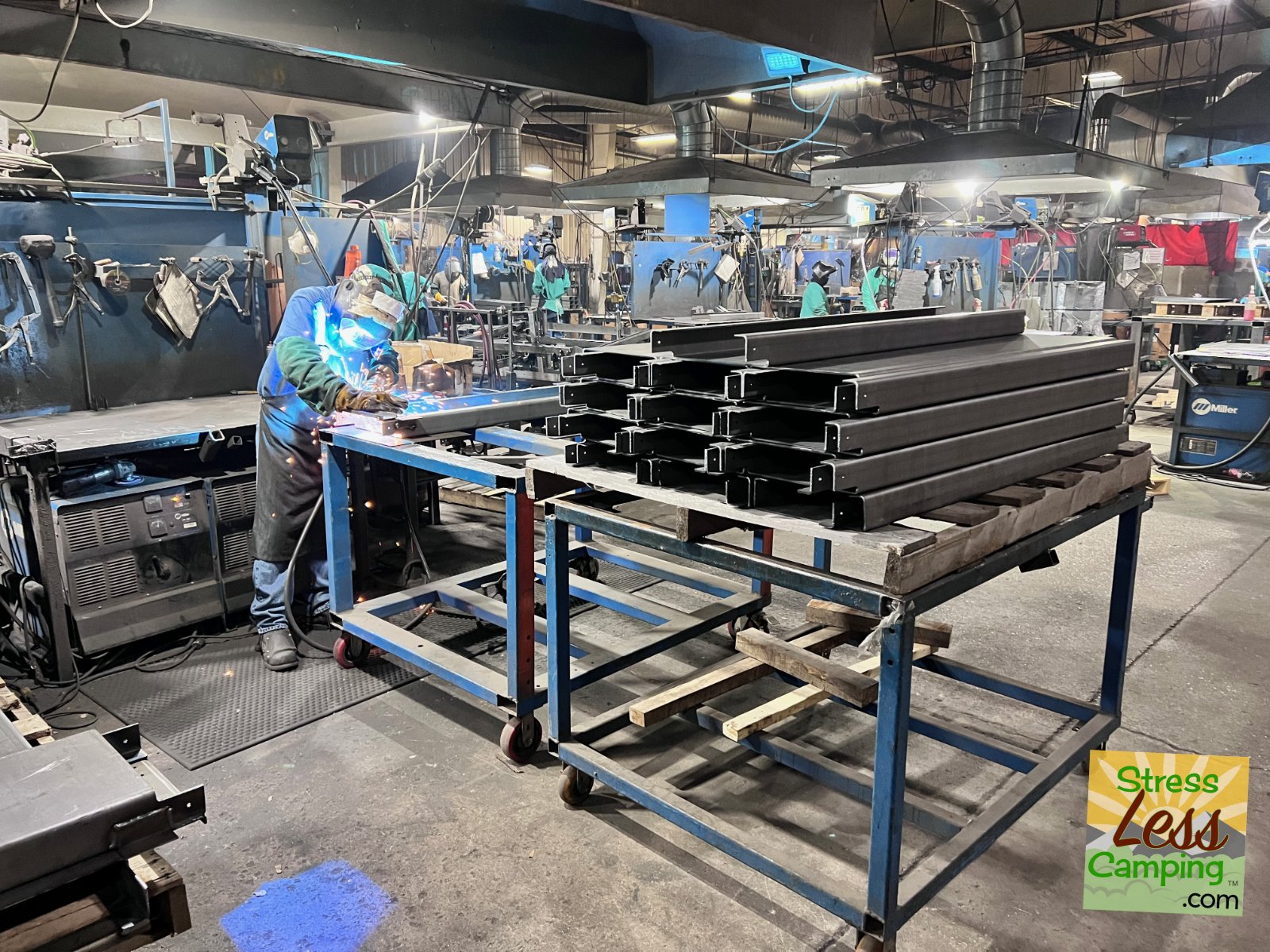
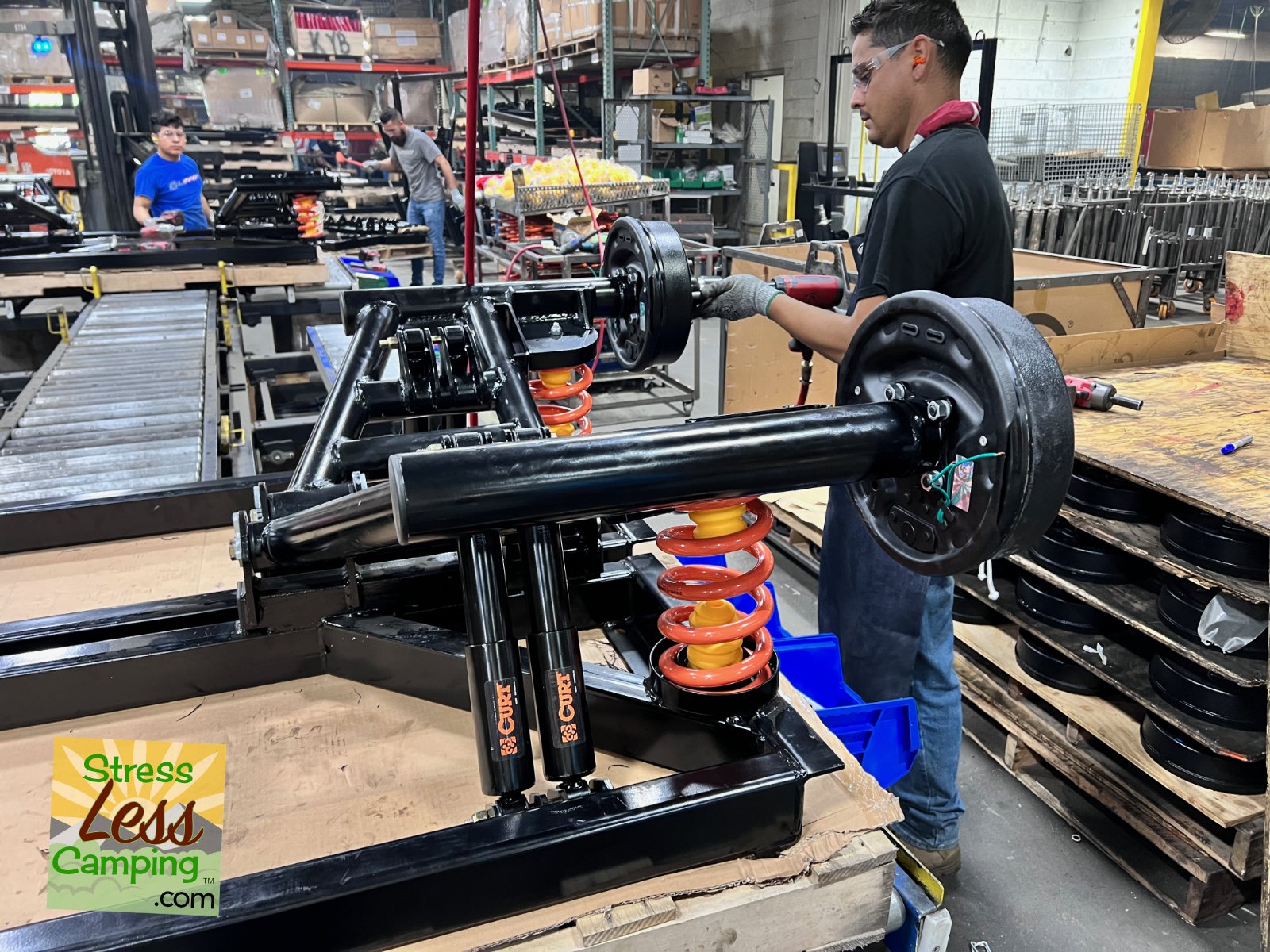
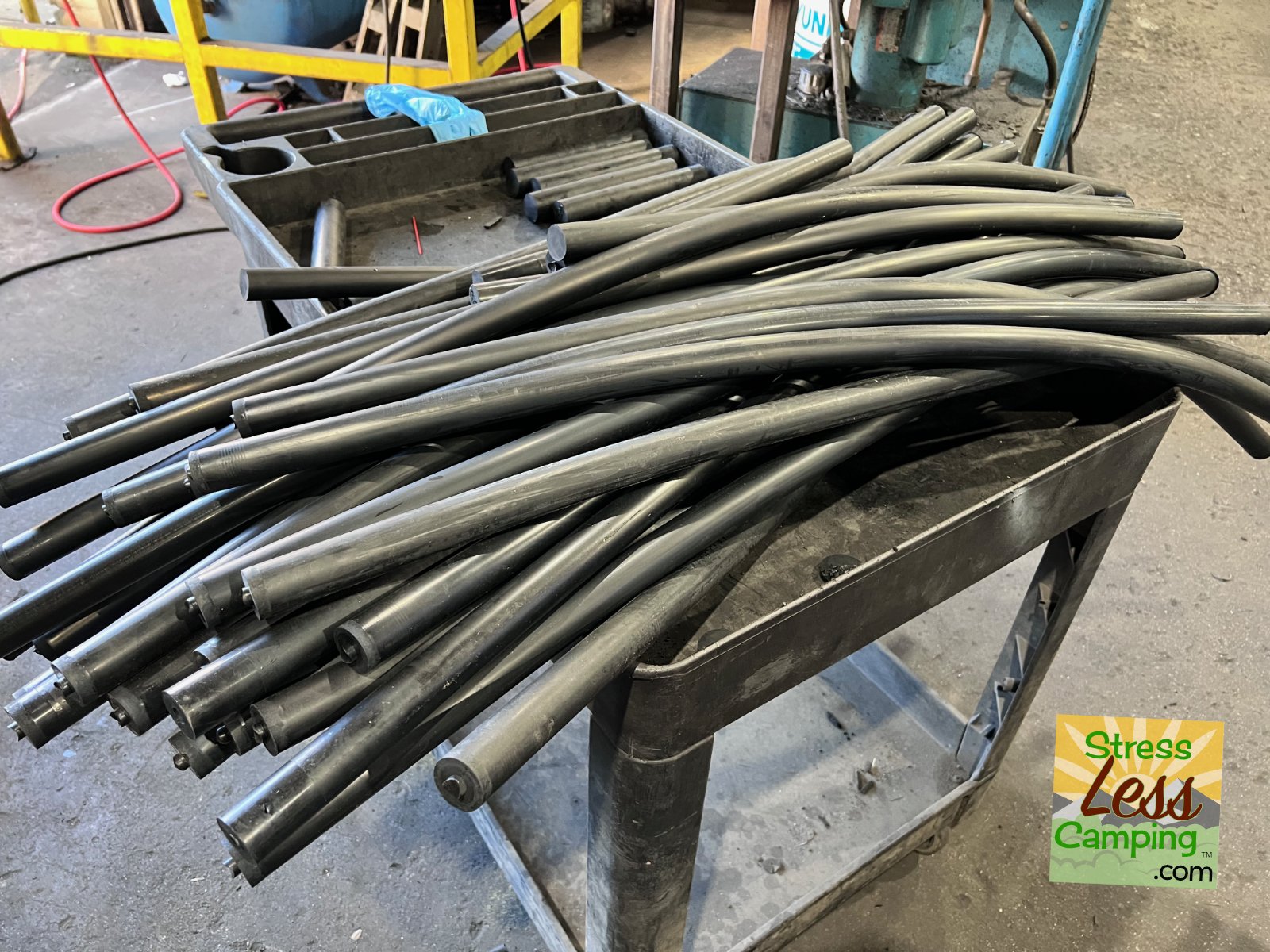
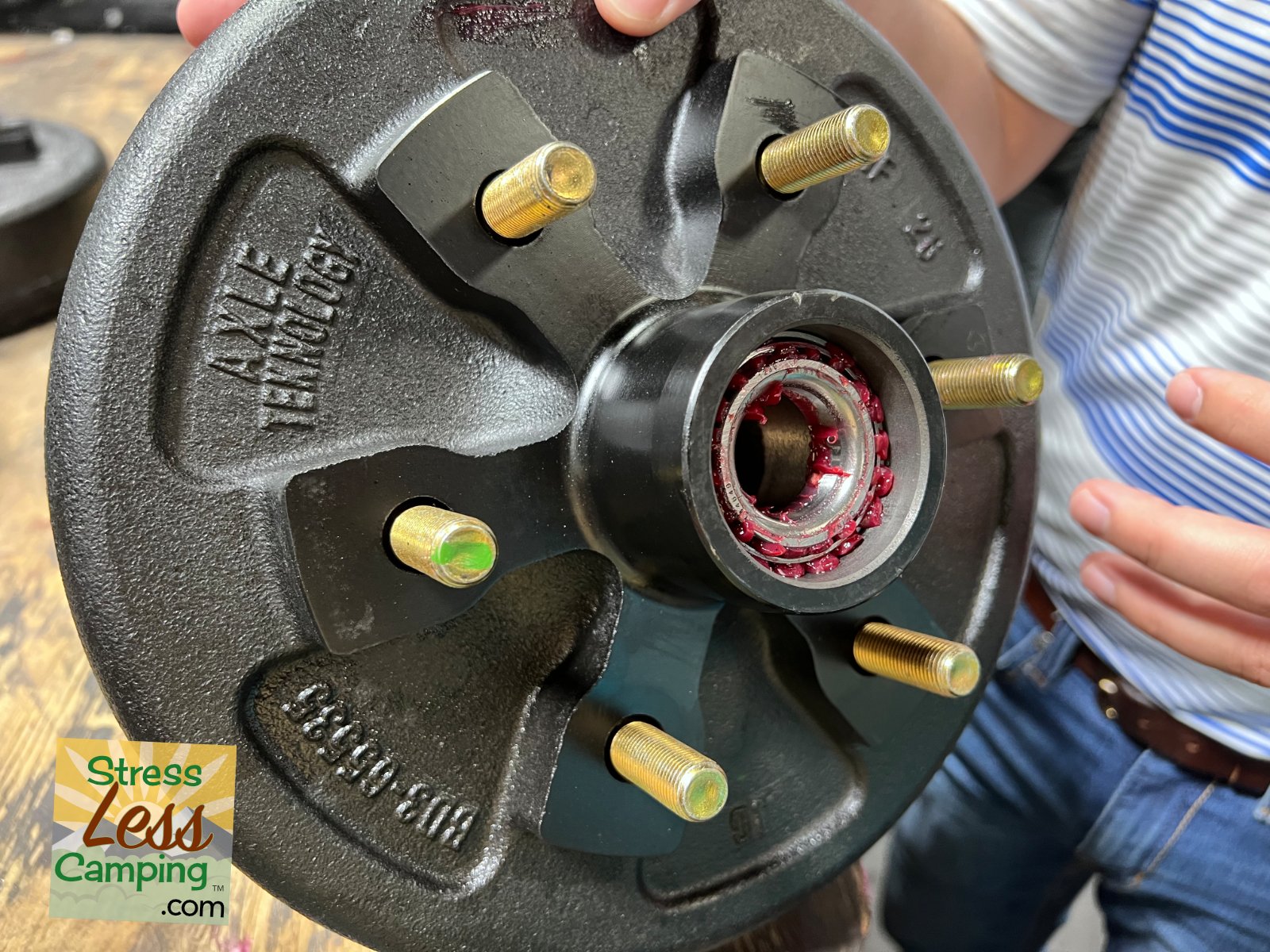
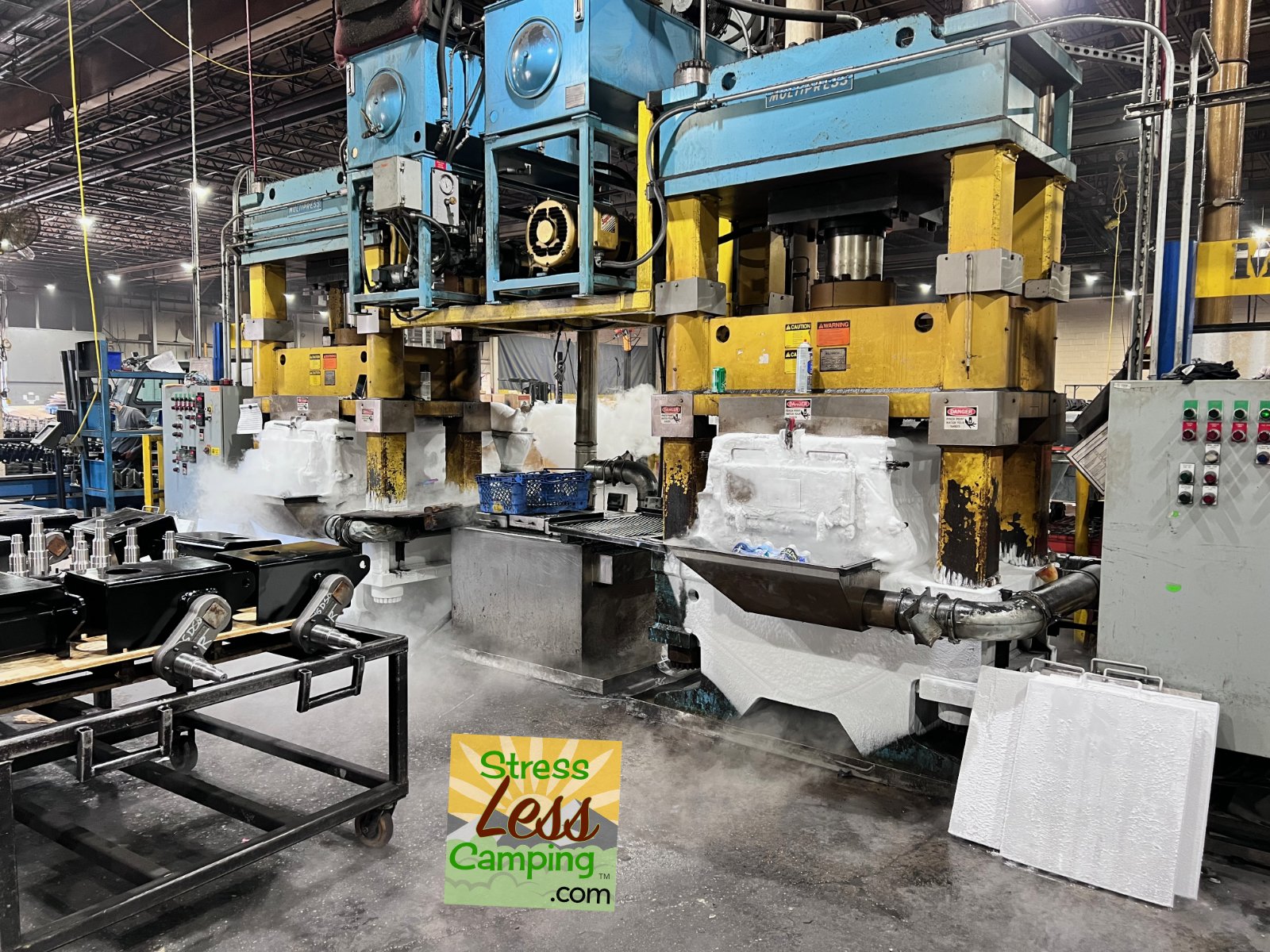
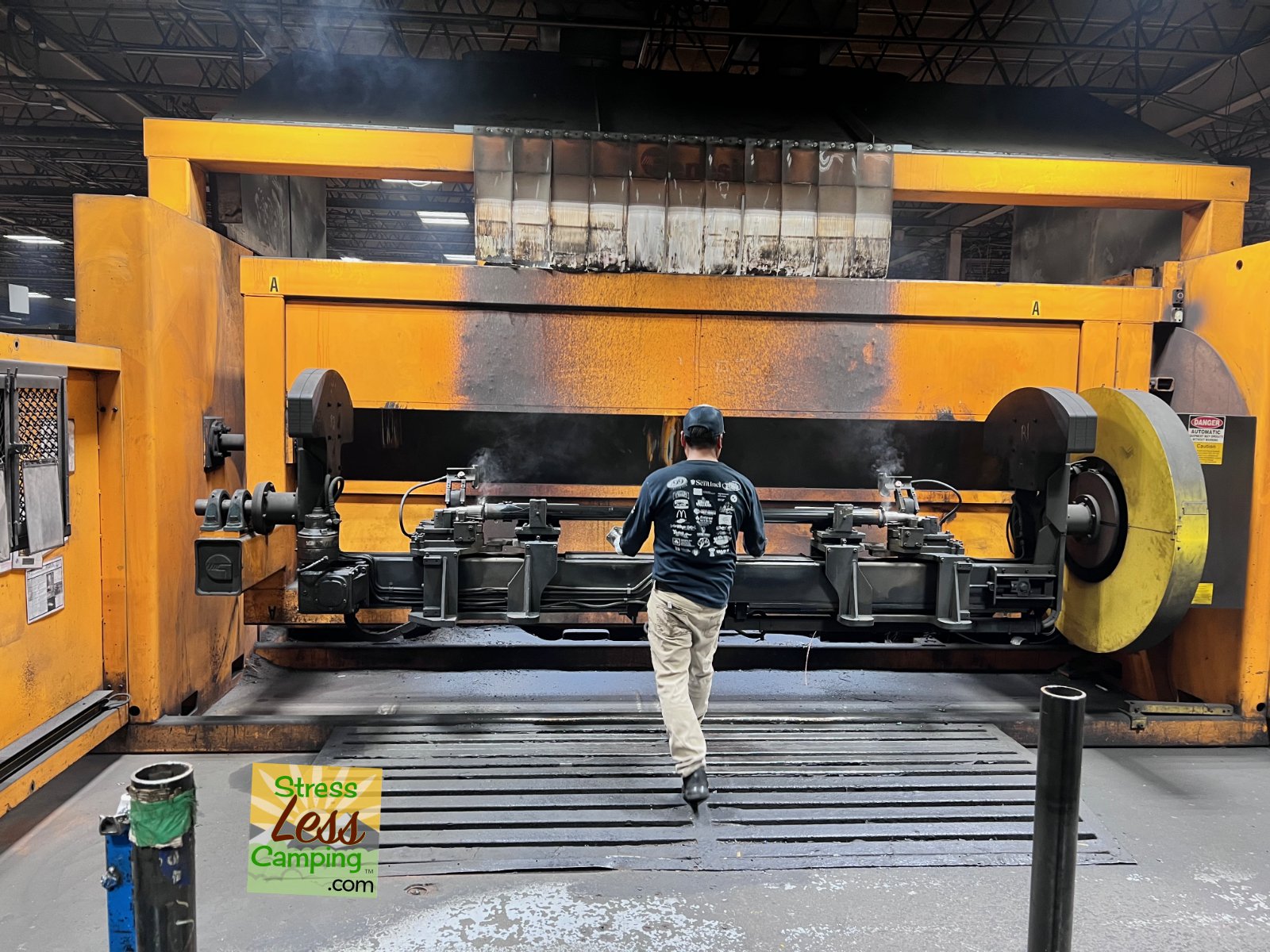
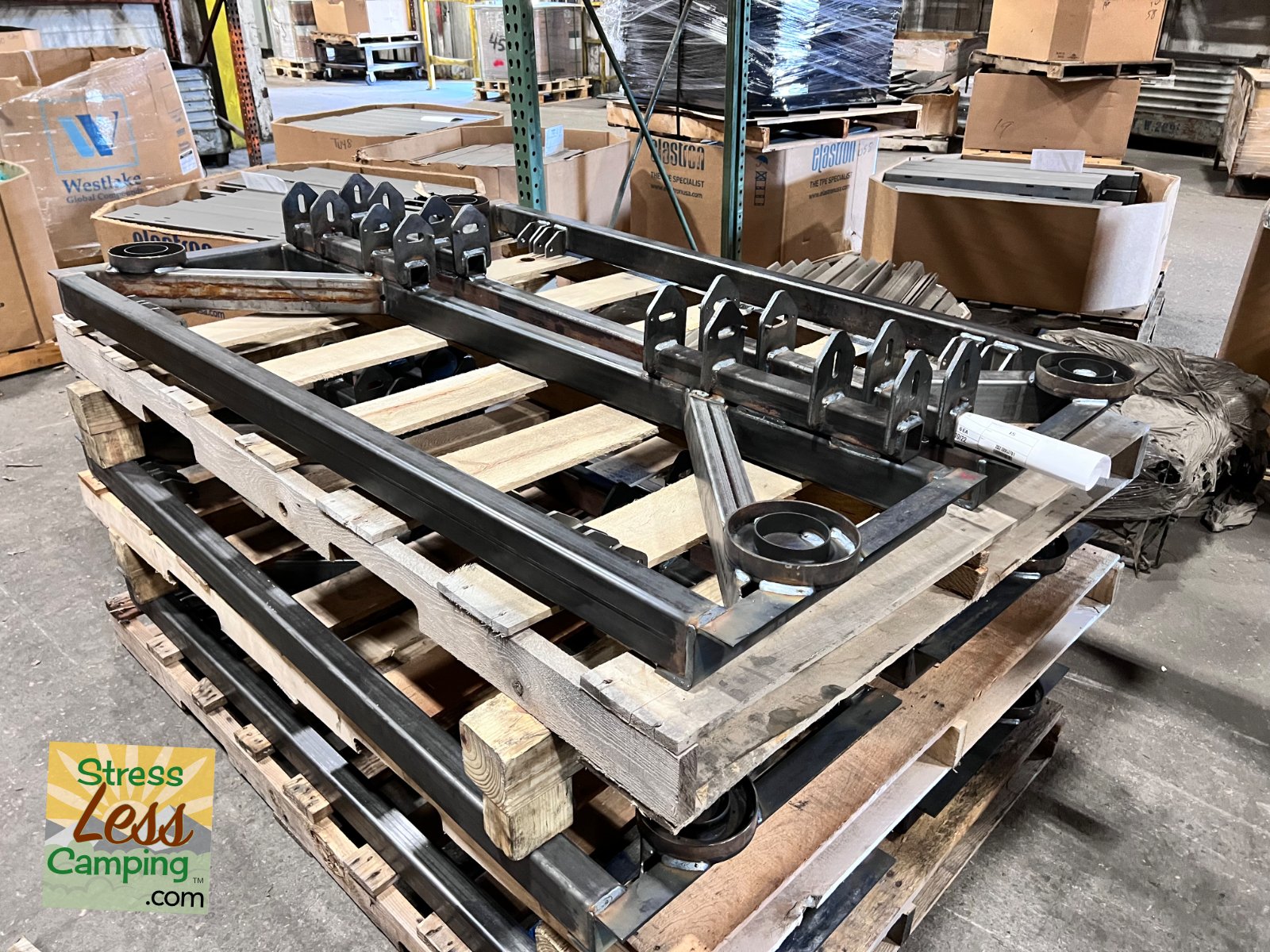
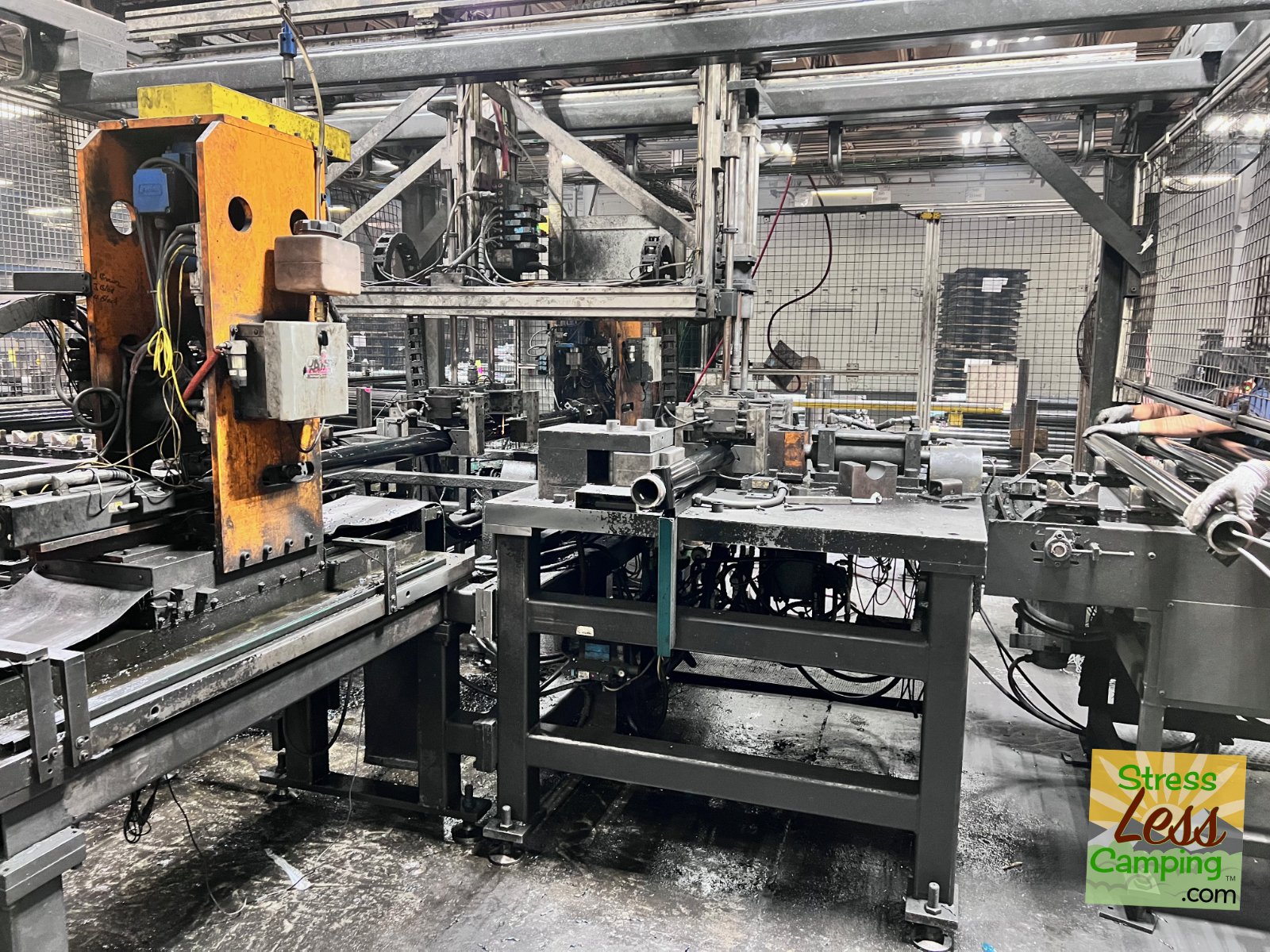
Torsion axle suspensions
This type of axle uses rubber tubes inside a steel axle tube as the suspension. It reportedly provides a smoother ride and also carries a much longer warranty. These types of axles go in some larger cargo trailers and horse trailers but are also used in some travel trailers and fifth wheels.
The way they’re built is by freezing the lengths of rubber in liquid nitrogen so they shrink and harden. Then the rubber and square center piece are pressed inside the tube and brought back up to normal room temperature.
Next level
Beyond the torsion axle, Lippert has developed an independent coil suspension system that uses springs and shocks much like an automotive suspension. These newer designs are used in all the Ember travel trailers and are finding their way to other brands such as Nobo, Ibex and rPod units.
We also got to see them being build and the subframe onto which they’re assembled is a significant piece of steel in an of itself. I’ve been told that the towing experience with these axles is terrific. Further, they’re well suited to those who like to travel off road.
My conclusion
Watching how well the team works together and the level of respect the line workers have for management, and vice versa, I can see why I’ve heard that Lippert is a good place to work. By keeping the team happy, they show-up and enjoy their jobs and do a better job.
Lippert is a unique company in that they’ll tailor make whatever the customer, the RV manufacturers, ask them to make within reason. This kind of flexibility and customer service truly can mean one brand of an RV can provide a much better experience than another even with components from the same supplier.
So, it proves that you do get your money’s worth and that it’s always good to shop carefully.
If you ever have a chance to tour any RV factory, do so. Touring these Lippert plants has given me a whole new appreciation for what the company does and also how they do it.